在许多人的观念中,“装配式建筑”就像搭乐高积木一样,将梁、板、柱、墙等构件,运到施工现场进行组装。
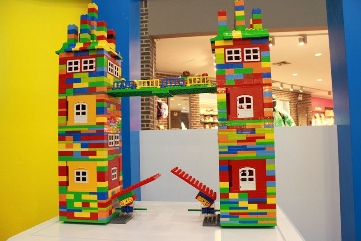
事实也是如此!传统的“装配式建筑”就是将若干在工厂事先做好的“二维平面式”构件在施工现场通过钢筋混凝土的搭接和浇筑,从而完成建筑的施工。自上世纪60年代以来,这种“产业化”、“工业化”的建筑在欧美及日本已经广泛采用。

随着科技的不断发展,世界已经进入了立体的“三维时代”。在“装配式建筑”领域,这种先进的生产技术在经历了多年的研发与实践后,也终于获得了实质性的进展,而这项技术的推动者就是来自中国的北京华商陆海科技有限公司(简称:华商陆海)。
接下来,我们就通过8张图,一起了解这种代表“装配式建筑”全球最先进工艺的生产过程。
首先,在“构件”的生产环节,以往的“装配式建筑构件”主要是通过传统浇筑工艺浇筑出平面的梁、板、柱、墙等构,这种生产方式最大的缺点就是构件的种类和数量的繁杂,从而给现场吊装带来了巨大的施工难度和安全隐患。
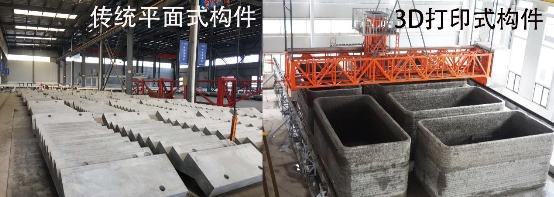
华商陆海的建筑构件,则是以“3D打印技术”为主要生产方式,以一体化成型的“单建筑”作为构件主体,从而不仅极大的降低现场吊装的工序,同时也大幅提升了建筑的抗震性。
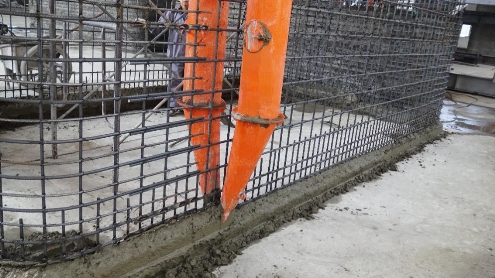
在构件的打印原材料方面,华商陆海所使用的是“普通标号的钢筋混凝土”,这也是当前全球最普及的建筑原材料。因此,这类建筑在“可居住性”方面,与咱们现在所居住的房子并无差别。
还有一点值得关注的是,全球能够以“普通标号的钢筋混凝土”为打印原材料的企业只有“华商陆海”,这也是这家企业的绝对技术壁垒。
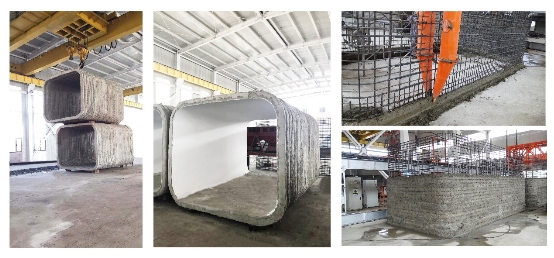
在构件的施工理念方面,华商陆海采用“竖着建、横着用”的理念,不仅能在施工过程中最优化的夯实建筑结构密度,增强建筑强度;同时还能在装配过程中,以“横着用”的概念扩大单体建筑的受力面积,增强了整体建筑的稳定性。
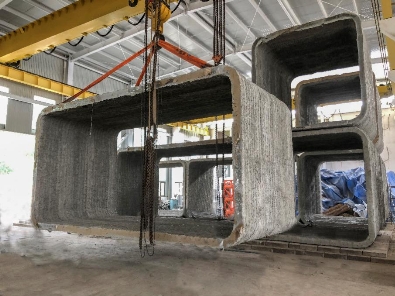
正是基于这种超强的建筑稳定性,在吊装环节中,华商陆海所打印的单重在几吨到数十吨的单体建筑,仅需4个吊点就能完成吊装工作。
除此之外,因为是单体建筑的构件,所以在吊装的过程中,对人为干预的“风险性”方面则有所降低,并且在装配的安全性方面也会更强。
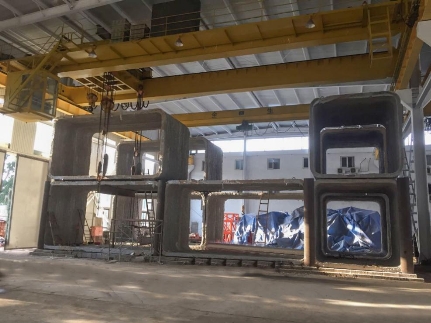
在现场装配环节方面,华商陆海的“3D装配式建筑”无需再进行“钢筋混凝土的搭接和浇筑”的工序,可直接通过框架固定完成主体结构的基础施工工作。这样,无疑又进一步降低了“人为干预”的风险性,提升了现场施工的效率。
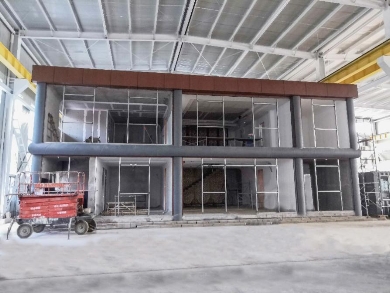
在“3D打印技术”的应用方面,华商陆海不仅使用在了主体建筑中的卧室、客厅、厨卫等功能区域,并且在园林设计方面也充分展现了该项技术的核心优势。
在这栋全球首个“3D装配式建筑”门前的景观造型中,华商陆海就使用了“3D打印技术”建造了一座具有江南风格的“单孔拱桥”。
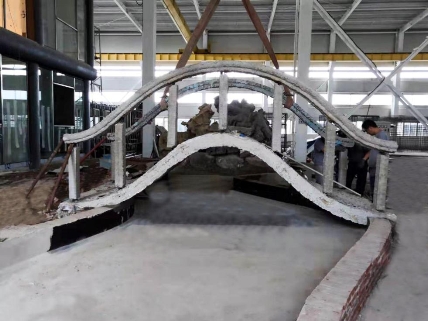
在施工周期方面,这座全部使用“3D打印技术”的“装配式建筑”,从构件打印到主体完工,实际施工的总时长仅有一个月。
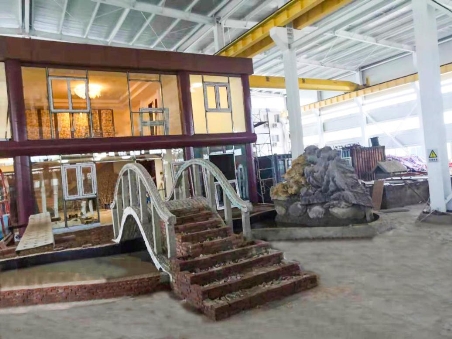
在成本投入方面,据华商陆海相关负责人介绍,这栋建筑的工程造价与传统的浇筑式并没太大差别,置业者完全能够承担。
相比较传统的“装配式建筑”,这种“3D装配式建筑”拥有三大“颠覆性”的技术优势。
首先,基于“3D打印技术”而建造的单体建筑构件,最大化的降低了现场装配过程中,人为干预的“风险性”。此前,我们在各大媒体上经常看到“装配式建筑”因施工人员在构件组装环节的疏忽而造成建筑质量隐患,这一点在“3D装配式建筑”施工环节中可最大化的避免。
此外,“3D装配式建筑”的单体建筑构件相比较传统的“板材式构建”,在建筑的结构稳定性和抗震性方面也将更好,不易出现传统“装配式建筑”墙面开裂、板材拼接缝隙不均、隔音效果不佳、保温隔热效果差等技术问题。
最后,就是这种建筑可实现“面积”和“格局”的自我升级。通俗概述就是,使用“3D装配式建筑”的置业者,未来如果想增大建筑面积或改变建筑的内部格局,不需要再“推倒重建”,直接吊装新的单体建筑或将已有的单体建筑重新吊装即可,这样将大幅的降低置业者在住房改善过程中的成本投入。
目前,这座全球首个“3D装配式建筑”已经进入了内部装修环节,预计将很快呈现在公众的面前。如果,您对这种全球最先进的建筑方式也有兴趣的话,可登录“华商陆海”的官网索取相关资料或预约参观。
文章来源:网络